Product Description
The ion nitriding furnace can process a variety of metal materials, including stainless steel, tungsten steel, high-speed steel, hardened steel, alloy steel, titanium alloy, aluminum alloy, etc. Among them, cemented carbide materials are commonly used. The materials treated by ion nitriding furnace are widely used in mechanical processing, aerospace, automobile, chemical industry, electronics and other fields.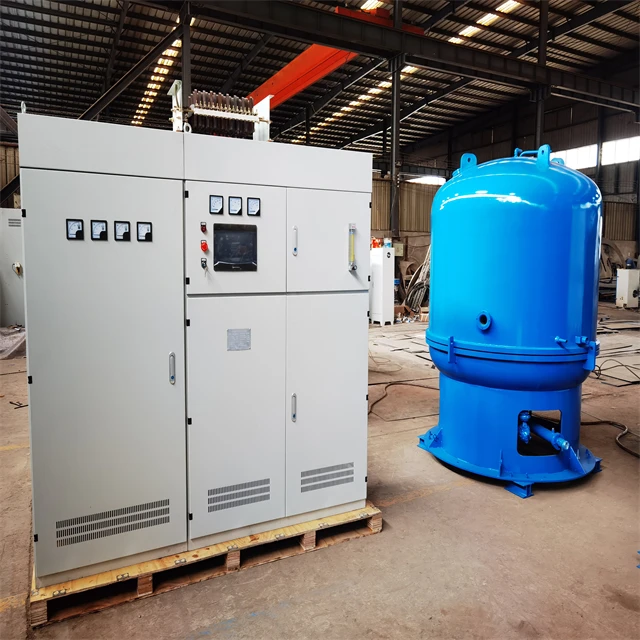
Components of ion nitriding furnace equipment:
1.a furnace body
2.Three-in six-out step-up transformer
3.A set of power cabinet
4.a vacuum pumpIon
Ion nitridation process flow:
1.Workpiece preparation
2.Place the workpiece on the workbench and close the furnace
3.Vacuum to 10mpa
4.Add voltage 400-600V
5.When the workpiece is heated to 100℃, add nitrogen and hydrogen (the amount of gas introduced is 801/h), and then rise the temperature to 520℃
6.Nitrogen atoms partially penetrate into the workpiece under the acceleration of the electric field, and hydrogen atoms combine with trace oxygen atoms to form water
7.The nitrogen atoms that are not involved are combined into nitrogen molecules, the hydrogen atoms that are not involved are combined into hydrogen molecules, the hydrogen atoms are combined with a trace amount of oxygen atoms to form water, and the three mixed gases are discharged from the furnace body through a vacuum pump
8.After 8-10 hours of heat preservation at 520 ℃, turn off the gas supply, turn off the vacuum pump, turn off the power supply, and the workpiece cools with the furnace
9.When the temperature of the workpiece drops below 200℃ , put air into the furnace to make the furnace reach atmospheric pressure, lift the furnace body, take out the workpiece, and finish nitriding.
Comparison before and after nitridation:
The main characteristics of ion nitriding are as follows:
1. Ion nitriding treatment is under the action of plasma electric field, nitrogen positive ions bombard the surface of the workpiece at high speed, so the penetration rate is very fast, about twice that of gas nitriding, and the processing time is shortened by about half; the processing cost is lower than that of gas nitriding ;
2. Compared with gas nitriding, the ion nitriding treatment can be nitrided at a lower temperature, the brittleness of the nitrided layer is small, and the deformation of the workpiece is small;
3. The gas consumption is very small, which is one tenth of the gas nitriding;
4. Unlike gas nitriding, which must be used with ammonia, ion nitriding can be used without ammonia and emit zero pollution;
5. The operation is simple, as long as the workpiece is evenly placed on the worktable, it can be nitrided after the furnace is closed;
6. Negative pressure type nitriding equipment, without any pressure danger;
7. Fewer external accessories, no need to use large gas buffer tank, small footprint;
8. The life of the furnace body is extremely long, up to more than 20 years.
Power cabinet detailsandFurnace body production parts:
item |
value |
Place of Origin |
HENAN |
Condition |
New |
Type |
Resistance Furnace |
Usage |
Heat Treatment Furnace |
Video outgoing-inspection |
Provided |
Machinery Test Report |
Provided |
Marketing Type |
Ordinary Product |
Warranty of core components |
1 Year |
Core Components |
PLC, Engine |
Brand Name |
IRIS |
Voltage |
380 |
Dimension(L*W*H) |
2800*1800*2050mm |
Weight (T) |
6.8T |
Power (kW) |
160 |
Warranty |
1 Year |
Key Selling Points |
Easy to Operate |
Applicable Industries |
Building Material Shops, Machinery Repair Shops, Manufacturing Plant, Food & Beverage Factory, Retail, Construction works , Energy & Mining |
Showroom Location |
None |
Item |
ion nitriding furnace |
Rated pulse current |
60A |
Ultimate vacuum degree |
6.7pa |
Maximum temperature |
650C |
Power output frequency |
1khz |
Vacuum degree when working |
50-300pa |
Power input voltage |
380V |
Pulse width duty cycle adjustment range |
5%-85% |
Furnace chamber size |
D1100*1200mm |
loading capacity |
1200kg (adjustable) |